Automatisation industrielle | 03/05/2018
Un entraînement ABB pour la boulangerie industrielle
Des solutions ABB dans le nouveau centre logistique de Coop à Schafisheim
Coop a construit un nouveau centre logistique à Schafisheim dans le canton d’Argovie. Il abrite entre autres la plus grande boulangerie-pâtisserie de Suisse. Différents processus de traitement y requièrent des températures très basses. C’est pour cela que sont utilisées quatre installations de réfrigération de la société Johnson Controls qui fonctionnent avec des moteurs et des convertisseurs de fréquence d’ABB.
Que l’on achète une salade pour le dîner sur le chemin de retour à la maison ou une brioche le samedi matin pour le brunch, nous sommes tous habitués à nous procurer les choses du quotidien au supermarché. Pour assurer la disponibilité de tous ces produits, une logistique parfaitement maîtrisée est nécessaire.
Si vous achetez votre brioche dans une filiale Coop de la zone de Zurich, dans le nord-ouest de la Suisse ou en Suisse centrale, elle provient de Schafisheim. On y trouve en effet un point de jonction important dans le réseau de distribution de cette société de commerce de détail. Coop a ouvert en 2016 dans le canton d’Argovie le plus grand centre logistique de la société après plusieurs années de travaux. Ce nouveau complexe immobilier regroupe le centre de distribution national de produits surgelés, un centre de distribution régional, mais aussi la plus grande boulangerie-pâtisserie de Suisse. 600 collaborateurs y produisent chaque année env. 60 000 t de pain, gâteaux, tartes et autres produits de boulangerie-pâtisserie à l’aide d’installations modernes. Ils sont par ex. en mesure de fabriquer 2000 brioches par heure, encore en partie tressées à la main.
La réfrigération joue un rôle important dans le processus de production. Au début, la pâte est placée dans de grands bacs pour y être pétrie à la machine. Sa température ne doit pas dépasser env. 24 °C. Pour s’en assurer, de l’eau froide comprise entre 0 °C et 1 °C y est versée. Après avoir divisé la pâte en portions et tressé les brioches, ces dernières passent dans un four emportées sur un tapis. La plupart des variétés de brioches sont simplement précuites. Elles passent ensuite dans un tunnel de pré-réfrigération. Le poste suivant est le congélateur. Les brioches y sont surgelées à env. -34 °C. Elles arrivent ensuite dans la centrale de congélation. Elles y séjournent à env. -24 °C avant d’être livrées aux filiales Coop et d’y terminer leur cuisson.
Une coordination précise du processus
Quatre installations de réfrigération assurent les basses températures nécessaires durant ces différentes étapes. Une première installation fournit l’eau froide utilisée pour le tunnel de pré-réfrigération et la climatisation du bâtiment. La deuxième traite l’eau glycolée froide à -7 °C et assure le froid dans les chambres froides de la boulangerie où sont stockés des œufs, du beurre et d’autres ingrédients. La troisième alimente le congélateur et la quatrième l’entrepôt réfrigéré. Ensemble, les installations fournissent une puissance de réfrigération de 8 MW, ce qui correspond à la puissance de plusieurs dizaines de milliers de réfrigérateurs. Les systèmes ont été conçus et installés par Johnson Controls.
La technologie d’ABB a elle aussi participé au projet: 18 moteurs IE4 d’une puissance comprise entre 132 et 355 kW, ainsi que 18 convertisseurs de fréquence ACS880 actionnent les compresseurs dans le circuit de refroidissement. Une qualité et une fiabilité maximales sont exigées à cet égard.
Il était important pour Johnson Controls de se procurer les moteurs et les convertisseurs de fréquence auprès d’un fournisseur unique. C’est le seul moyen d’avoir un ensemble parfaitement coordonné. «L’équipe d’ABB nous a très bien conseillé et est restée à nos côtés tout au long du projet. Elle a par exemple étroitement contrôlé la configuration avant la mise en service. C’est une condition préalable importante pour que tout fonctionne correctement ensuite», explique Beat Schuppisser, Branch Manager Froid industriel chez Johnson Controls et chef de projet général pour les installations de réfrigération. Andreas Kreienbuehl, responsable chez ABB souligne aussi l’importance de la collaboration: «Nous avons étudié en détail les demandes de Johnson Controls et avons optimisé les systèmes en conséquence.»
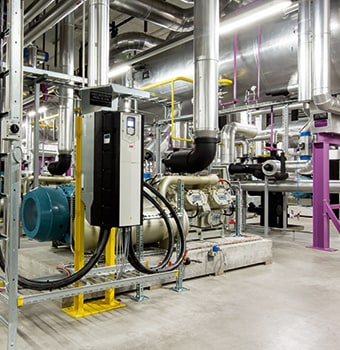
Coop
Le groupe Coop est profondément ancré en Suisse où il existe depuis 150 ans. Ce qui n’était au départ qu’une petite coopérative est aujourd’hui devenue une société internationale de commerce de détail et de gros.
Johnson Controls
propose des produits dans le domaine de la technologie du bâtiment et du stockage de l’énergie. La technologie du bâtiment couvre les techniques de refroidissement et de CVC, l’immotique, les techniques de sécurité et la protection anti-incendie. Plus d’un million de clients dans plus de 150 pays utilisent ses solutions avancées, profitant d’une plus grande performance énergétique et d’un meilleur rapport coût-efficacité.
Une grande performance énergétique
La durabilité est déterminante pour tout le centre logistique. Une installation photovoltaïque fournit par ex. de l’énergie électrique pour les différents consommateurs du complexe immobilier. La liaison de transport de marchandises par le chemin de fer a par ailleurs été optimisée. La chaleur des fours de la boulangerie est en grande partie délivrée par une centrale de chauffage biomasse locale. Au total, Coop réduit les émissions de CO₂ de plus de 10 000 t avec la mise en service du centre.
La performance énergétique des installations de réfrigération était tout aussi importante. Les moteurs ABB sont classés IE4, la classe de rendement la plus élevée, et présentent un rendement de 97%. Des économies d’énergie supplémentaires sont réalisées grâce aux convertisseurs de fréquence: ils varient avec précision la vitesse des moteurs en fonction de la puissance de réfrigération nécessaire.
Beat Schuppisser est très satisfait du projet dans l’ensemble: «Nous avons mis en place une installation à la pointe de la technique, dont la performance énergétique est optimale. L’ensemble de moteurs IE4 et de convertisseurs de fréquence est ce que l’on a de mieux dans ce domaine», précise-t-il. Les installations de réfrigération fonctionnent parfaitement depuis la mise en service un an auparavant. La brioche sortie des rayons de Coop que vous dégustez a pu voir le jour grâce à d’habiles mains, mais aussi une technique moderne.
«L’ensemble de moteurs IE4 et de convertisseurs de fréquence est ce que l’on a de mieux en matière de performance énergétique».
Solutions ABB dans le centre logistique de Coop
Le nouveau complexe immobilier abrite des moteurs, des convertisseurs de fréquence et bien d’autres produits ABB:
Robots industriels
Chaque jour, des milliers de caisses de transport vides sont retournées par près de 400 filiales Coop vers le centre de récupération d’emballages vides près de Schafisheim. 15 robots ABB de type IRB 2600 et IRB 6700 déchargent les caisses des conteneurs de transport, les trient et les empilent. Un IRB 360 FlexPicker se trouve également dans la boulangerie: il y exécute plusieurs étapes du processus de travail de la pâte.
Onduleurs solaires
L’installation photovoltaïque située sur le toit produit chaque année environ 250 000 kWh d’énergie électrique pour ses propres besoins. Sept onduleurs solaires ABB PRO-33.0 transforment le courant continu en courant alternatif et l’injectent dans le réseau de distribution d’énergie du centre logistique.